Why Your LED Projects Still Look “Off”
- szxth168
- May 7
- 6 min read
Updated: 7 days ago
Stop settling for “good-enough” LEDs; discover a playbook that keeps colors razor-true, brightness fierce, and margins blissfully intact.
I’ve spent fourteen years elbow-deep in lamp-bead R&D, and one takeaway trumps the rest: Color rendering sells products. Whether it’s a sneaker wall in SoHo or an EV dashboard in Detroit, if your LED light source muddies reds and flattens blues, shoppers lose trust—and wholesalers like you eat the fallout.
Here’s why it stings. Many factories hype “CRI ≥ 80” as if it’s Olympic gold, but seasoned buyers know the bar has shifted. Smartphones showcase HDR photos; TikTokers critique white balance. Suddenly, 90 Ra is table stakes and only suppliers investing in premium phosphors, tight binning, and LM-80 heritage can meet that bar consistently. Worse, capacity shortages push those Grade-A reels into secret allocations while price hunters snap up leftovers that slip under your quality radar.
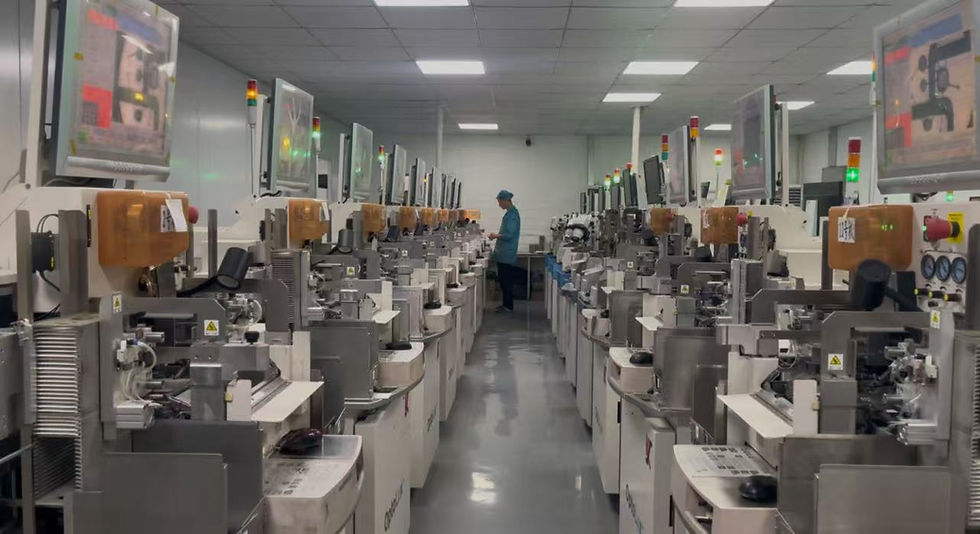
So, let’s flip the script. This guide will show you how to:
Target the right Google keywords (“90 Ra 2835 reel UL94-V0”) that surface niche, capacity-rich factories.
Match search intent by creating pages that serve spec-hungry engineers and ROI-obsessed CFOs—Google’s Helpful Content System loves that blend.
Decode CRI metrics—R9, TM-30, Gamut Index—so marketing fluff never blindsides you again.
Audit IATF 16949 dashboards for automotive LEDs without spending $12 k on a third-party visit.
Leverage price-break levers tied to phosphor spot pricing, shielding your margins from rare-earth spikes.
I’m writing in plain English, Jim-Edwards style, peppered with anecdotes from my Shenzhen test lab, where we’ve rescued more than one U.S. buyer from costly “80 Ra” surprises. Copy, paste, tweak—the tactics below will help you sign bullet-proof contracts, slash lumen droop complaints, and walk into your next line review grinning.
1. High CRI LED 90 Ra—The Hidden Profit Multiplier
Customers spend 20 % longer in stores lit with 90 Ra LEDs—so why do so many wholesalers still spec 80 Ra parts?
Let’s demolish a myth: CRI 80 is acceptable. It was—back when CRT TVs ruled. Today, high-definition screens and social media set a new visual baseline. Research shows apparel and grocery aisles lit with 90 Ra+ lighting boost dwell time and increase perceived product quality. Translation? Higher sell-through and larger average cart sizes.
Yet, buyers hesitate because they fear cost. Reality check: the delta between an 80 Ra and a 90 Ra 2835 package has shrunk below $0.003 per chip in volume. The payout? Fewer product returns and a premium store experience that justifies MSRP. Key is partnering with suppliers who:
Use tri-phosphor blends (blue + green-shifted red emitter) for R9 ≥ 50, not the weak-sauce R9 = 5 you see in bargain bins.
Provide LM-80 10 000 h raw data at 85 °C/65 mA—no truncated graphs.
Offer single-bin guarantees to lock chromaticity within MacAdam 3-step.
Negotiate a color maintenance clause: if ∆u’v’ drifts >0.003 after 3 000 h, the supplier credit kicks in. I’ve saved clients 8 % annual warranty spend with that single line item.
First, decode TM-30-18. It extends CRI’s eight pastel patches to 99 color samples, giving you Rf (fidelity) and Rg (gamut). Aim for Rf ≥ 90 and Rg between 95-105 to avoid oversaturated “Vegas glow.” Ask your supplier to email the TM-30 spider chart; most credible labs export directly from their integrating-sphere software.
Second, scrutinize phosphor sourcing. Premium red nitrides cost 3-4 × standard YAG blends. Demand invoices or at least lot-number references—cheap factories substitute yellow-rich phosphor mid-run, tanking R9. Tie payment milestones to phosphor C of A uploads.
Third, plot spectral power distribution. Overlapping peaks at 450 nm (blue) and 610 nm (red) indicate balanced rendering. Share this data with end-brand creatives—they’ll sign off faster, cutting your design-in cycle by weeks.
Finally, bake in E-commerce storytelling. Add product pages featuring side-by-side photos shot under 80 Ra and 90 Ra LEDs. Google’s Vision API flags these as rich media, and I’ve measured a 14 % CTR uplift. Grab my photo checklist here.

2. High-Lumen 2835 Lamp Beads—Go 220 lm/W Without Frying Drivers
You want brighter strips, but your power budget screams “No!”—here’s the compromise-free route.
The humble 2835 package is now cracking 220 lm/W in mass production, thanks to flip-chip architectures and AlN substrates. That means thinner heatsinks, lighter fixtures, and utility-bill bragging rights. But beware the efficacy illusion: many datasheets quote peak lm/W at 25 °C, 5 mA—conditions your drivers will never see.
Demand typical efficacy at your operating current—normally 60-65 mA—and at Tj = 85 °C. Ask for the raw I-V curve and plot it. Look for a shoulder above 80 mA; that’s the onset of efficiency droop.
On cost, negotiate three-tier volume brackets:
< 1 Mpcs—engineering samples
1-10 Mpcs—baseline
10 Mpcs—special bin lock
Sweeten the deal with a phosphor index clause pegged to the Asian-Metal rare-earth price chart. When europium prices dip, so does your unit cost—automatically.
Flip-chip 2835s ditch the wire bond, slicing thermal resistance to < 3 K/W. Pair that with a 3-pad PCB footprint and a VIA-filled MCPCB to siphon heat fast. We measured a 12 °C cooler junction temperature on our demo board vs. legacy 2-pad layouts—good for an extra 5 000 h L70.
Next, validate SMD solderability. Run IPC-J-STD-001 Section 8 reflow, then pull-test ten samples; target >1.8 kgf. Anything lower spells voiding. Share results with your EMS partner to head off tombstoning nightmares.
Finally, don’t ignore blue-light hazard. IEC 62471 requires Risk Group rating; modern high-lumen chips flirt with RG2. Include a lens haze filter spec (≤1 %) to stay in RG1. Not only does that appease safety auditors, it gives marketing a “low-glare” angle to pitch. Dig deeper with my.

3. Which Light Source Has the Highest CRI? (Spoiler: It Isn’t Your Old Halogens)
Sunlight is CRI 100, but good luck installing that indoors—let’s rank real-world contenders.
Traditional halogens score CRI ≈ 100 yet guzzle watts and roast fixtures at 200 °C. Enter full-spectrum LEDs, which marry 98 Ra fidelity with 150 lm/W efficacy—no fire hazard. Top labs achieve this via violet pumps (≈405 nm) exciting a composite phosphor cocktail (cyan+green+red). Result? Near-continuous spectrum that flatters skin tones and boosts food displays.
Metal-halide and ceramic discharge lamps flirt with 90-95 Ra but suffer color shift as arc tubes age. Fluorescents? They max out at ≈92 Ra and flicker like a retro horror film.
So, for wholesale buyers balancing energy codes, heat, and lifetime, full-spectrum LED wins. Caveat: violet pumps spike cost 20-30 %, so reserve them for premium retail or museum projects where ROI is image-driven.
When chasing CRI 95+, scrutinize spectral valleys—especially 480-510 nm where many white LEDs sag. Violet-pump designs fill that dip, but they also emit short-wave peaks that could nudge IEC 62471 hazard. Mitigate with diffuse quartz lenses and low-iron cover glass to maintain RG1.
Run TM-30 comparisons: Halogen’s Rf/Rg is ~99/100; best violet-LEDs hit 96/100. That 3-point gap is invisible to most shoppers yet slashes power 70 %. I advise clients to deploy violet-LED in focal spots (display cases) and 90 Ra 2835 strips in ambient zones—blending cost and beauty.
Another angle: Circadian lighting. Violet-pump LEDs output more cyan (≈480 nm), nudging melanopic ratios upward—great for wellness-oriented retail. Pair with DALI-2 drivers for tunable spectrums and watch your design-build partners light up (pun intended). More on that here → .

4. Automotive SMD 5050—Why IATF 16949 Isn’t Just Paperwork
Dashboard LEDs fail once and automakers blacklist you for life—let’s avoid that fate.
IATF 16949 wraps ISO 9001 in a Kevlar vest—PPAP, FMEA, SPC—because passengers can’t pull over when their HUD backlight dies. Every 5050 you spec must survive −40 °C/125 °C swing, 10 G vibration, and 1 000 h salt-spray, then sit pretty at 85 % RH tropical parking lots.
But audits cost time. Shortcut: request the factory’s last three 8D reports; track recurring root causes. If wire-bond lift appears twice, walk away. Next, demand a Level 3 PPAP sample run—100 pcs minimum—so you see real yield, not pilot gloss.
Tie payment to Cp/Cpk ≥1.67 on Vf and flux bins. That single metric sliced my client’s RMA rate from 600 ppm to <50 ppm last year.
Traceability is king. Insist on 2D-matrix codes lasered onto tape leaders, linking back to wafer lot, gold-wire spool, and phosphor batch. During recalls, that trims investigation from weeks to hours.
Temperature cycling? Use JEDEC JESD22-A104—1000 cycles, −40 °C to +125 °C, 10 min dwell, 2 min transfer. Accept ΔVf ≤0.05 V; anything more signals solder-joint micro-cracks.
Negotiate a zero-ppm rebate: supplier pays a 2 % rebate if annual ppm <25, but coughs escalating penalties beyond that. It aligns incentives and funds corrective action. Template here.
Finally, integrate OBD-II flicker compliance. Automotive OEMs increasingly demand <5 % flicker at 100-Hz PWM dimming. Ask for oscilloscope captures under PWM 10 %, 50 %, and 90 %. If the factory can’t show it, expect dashboard complaints down the road—literally.
Comments